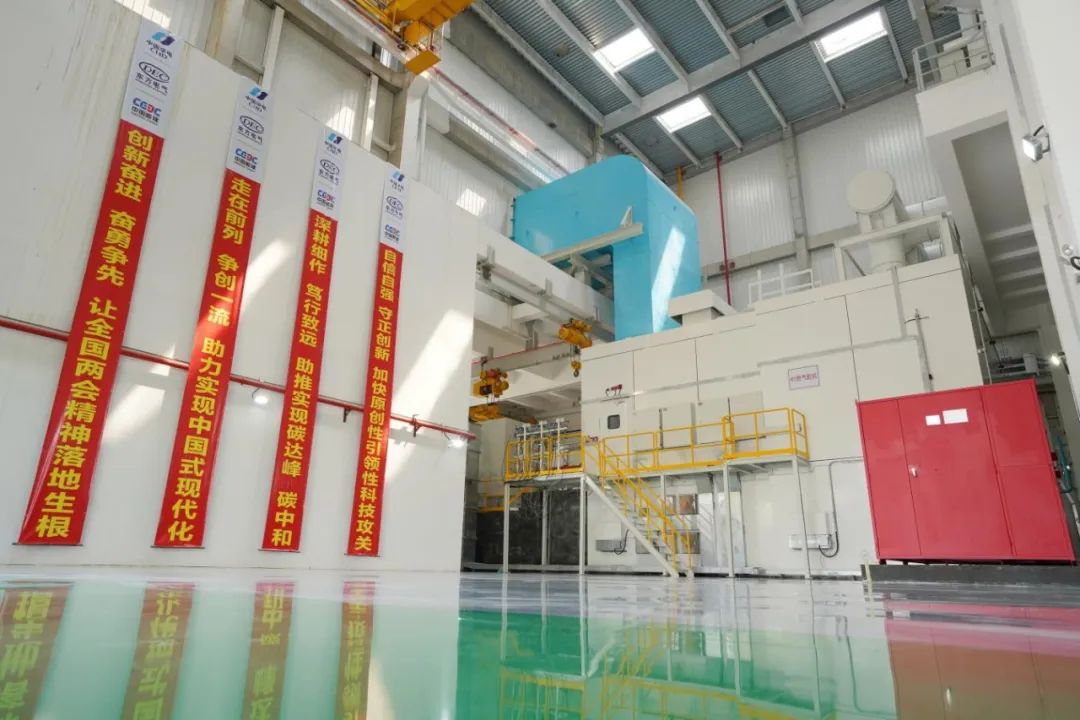
▲華電清遠華僑工業(yè)園天然氣分布式能源站現(xiàn)場。楊璽/攝
3月8日,被譽為中國“爭氣機”的我國首臺全國產化F級50兆瓦重型燃氣輪機商業(yè)示范機組在華電清遠華僑工業(yè)園天然氣分布式能源站順利通過了“72+24小時”試運行。
該機組研制、安裝、調試工作圓滿完成,各項性能指標達標,正式投入商業(yè)運行,填補了我國自主燃氣輪機應用領域空白,解決了多項“卡脖子”關鍵核心技術難題,為清潔能源領域提供了自主可控全鏈條式的“中國方案”,開啟了中國自主燃氣輪機產業(yè)高質量發(fā)展的新篇章。
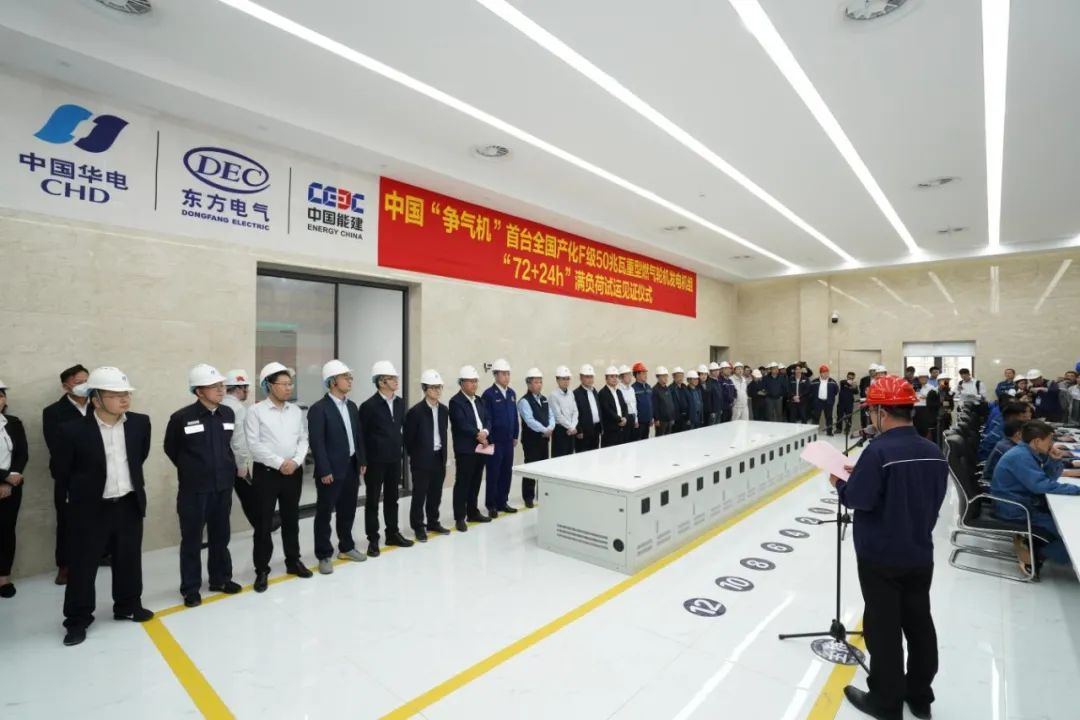
▲首臺全國產化F級50兆瓦重型燃氣輪機發(fā)電機組“72+24小時”滿負荷試運見證儀式現(xiàn)場。楊璽/攝
堅持高水平科技自立自強
重型燃氣輪機被譽為工業(yè)裝備制造業(yè)“皇冠上的明珠”,要讓設備在高溫、高壓、高轉速的條件下安全運行,所需知識涉及氣動力學、固體力學、燃燒學、機械學、材料學、自動控制等多個學科。
為服務國家重大戰(zhàn)略,由國務院國資委牽頭,東方電氣和中國華電等中央企業(yè)強強聯(lián)合解決能源領域重大裝備問題。國家能源局也將F級50兆瓦重型燃氣輪機列為能源領域首臺(套)重大技術裝備示范項目。
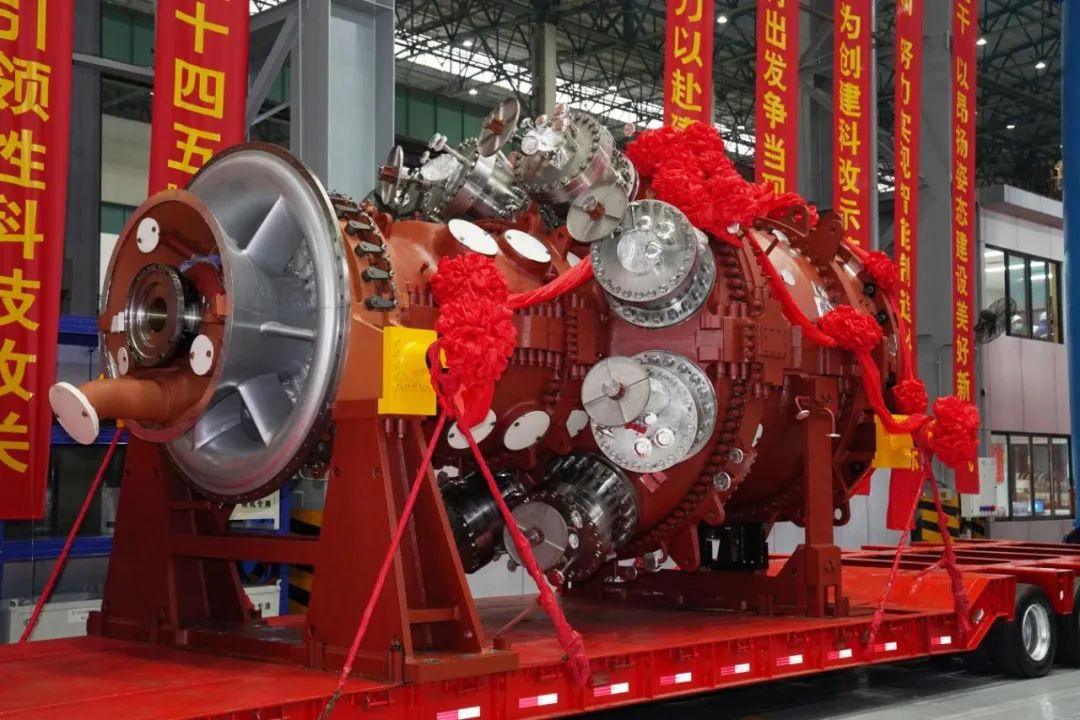
▲東方電氣集團自主研制的國內首臺F級50兆瓦重型燃氣輪機發(fā)運。楊璽/攝
東方電氣自2009年開始,歷時十三載自主研制,累計投資近20億元,率先在國內開展具有完全自主知識產權的F級50兆瓦重型燃氣輪機研制。2016年建成國內首批壓氣機、燃燒器、透平部件級試驗臺;2018年相繼研制成功壓氣機、燃燒器;2019年實現(xiàn)全部高溫部件100%自主制造,整機點火試驗一次成功;2020年首次運行至100%負荷;2022年底在華電清遠實現(xiàn)一次點火成功;2023年正式轉入商業(yè)運行。
東方電氣解決了“卡脖子”關鍵核心技術難題,實現(xiàn)“0”到“1”的突破,全面攻克了燃氣輪機自主研制、試驗全過程技術,建設了自主的F級燃機設計體系,掌握了燃氣輪機核心部件與整機總體性能、總體結構的設計方法。同時,構建了自主知識產權的設計規(guī)范、軟件和數(shù)據(jù)庫,獲得授權發(fā)明專利136項,參與制訂了國家/行業(yè)標準6項,形成了燃機設計/制造標準超1000項,建成了行業(yè)唯一的清潔高效透平動力裝備全國重點實驗室,F(xiàn)級50兆瓦重型燃氣輪機更是兩次獲評“央企十大國之重器”。
中國華電深耕燃氣發(fā)電機組運行、維護、檢修二十載,是國內燃機裝機容量最大、機型最全、覆蓋區(qū)域最廣的能源電力央企,在燃機運行管理、檢修維護、技術服務、國產控制系統(tǒng)研制等方面經驗豐富,掌握著重型燃氣輪機控制系統(tǒng)自主設計、生產、調試、改造等全過程關鍵技術。華電清遠項目便采用了中國華電自主研發(fā)的“華電睿藍”自主可控TCS、DCS全廠一體化控制系統(tǒng),提升了核心控制裝備自主化水平和技術安全性,保障了基礎設施安全穩(wěn)定運行,促進了國產軟硬件生態(tài)系統(tǒng)健康發(fā)展。
攜手推動產業(yè)鏈自主可控
東方電氣和中國華電將推動產業(yè)鏈創(chuàng)新鏈深度融合作為央企使命。2021年將東方電氣F級50兆瓦重型燃氣輪機應用到華電清遠項目上,全力攻克自主燃機示范應用難題。
在研制過程中,東方電氣堅持“燃機主機裝備必須國產化、沒有國產化的加快實現(xiàn)國產化”的基本原則,聯(lián)合高校、設備供應商、用戶等產業(yè)鏈上中下游近300家單位開展聯(lián)合攻關,突破了燃機材料選型、研制、控制、試驗等多項“卡脖子”難題,成功具備了燃機整機和全部部件研制能力,建成了完備的燃機試驗驗證平臺,培育了一批“專精特新”企業(yè),培育了一條完整的燃機國產化供應鏈,確保燃機產業(yè)鏈自主可控、安全可靠。
在項目建設的過程中,中國華電全面踐行“創(chuàng)新奮進、奮勇爭先”的企業(yè)文化,堅持進度與質量安全相統(tǒng)籌,在數(shù)十次燃機點火燃料程序優(yōu)化試驗中積累數(shù)據(jù),高質量地完成了首臺套G50裝備在華電清遠落戶安家、并網發(fā)電的任務目標,創(chuàng)造了25天完成燃機安裝、從開工到并網僅9個月的“中國速度”。創(chuàng)新使用全國產化中高溫脫硝催化劑、國產化大容量發(fā)電機出口斷路器,為燃氣電廠重要主輔機全方位“中國造”提供了“華電路徑”。