中國的西部,世界的東方,這里是坐落在天府之國的東方電氣集團。
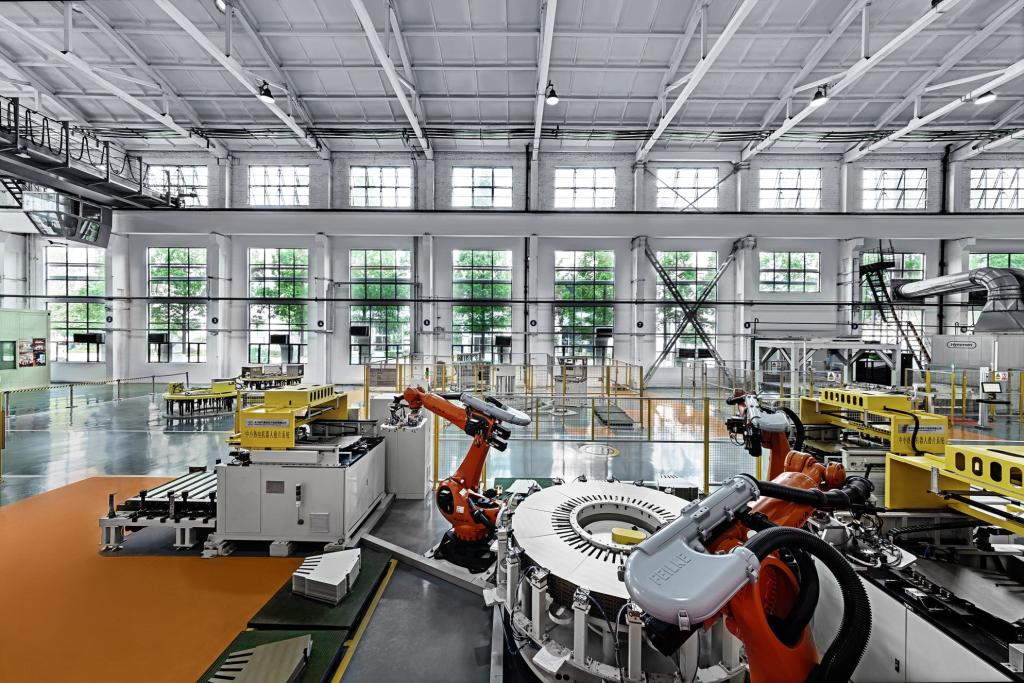
定子沖片綠色無人車間機器人疊片 東方電機供圖
1959年,在德陽西街的一間民房里,東方電氣集團首家企業(yè)——東方電機克服缺少資源、沒有設備等困難,造出了第一臺電機。
1979年,東方電機成功研制了迄今世界上轉輪直徑最大的葛洲壩170兆瓦軸流轉漿式水電機組,1981年機組并網(wǎng)發(fā)電,1985年獲得了首屆國家科學技術進步獎特等獎。
如今,東方電機清潔能源裝備重型制造數(shù)字化車間,云集了一批中國乃至世界一流的加工設備,由于其超大的規(guī)模和超強的制造能力,曾被譽為“中華第一跨”。
東方電機成功研制三峽水電站700兆瓦水電機組,從左岸到右岸,從跟跑到并跑,東方電機為三峽大壩裝上了“中國心”,實現(xiàn)了“中國裝備,裝備中國”的新跨越。
除了舉世矚目的三峽、溪洛渡、白鶴灘等巨型水電機組,臺山175萬千瓦核能發(fā)電機組、華龍一號、國和一號核能發(fā)電機重要部件都產(chǎn)自這里。
9月20日,澎湃新聞(www.thepaper.cn)跟隨國務院國資委新聞中心,走進東方電氣集團,打卡中國新坐標,深入了解東方電氣集團里程碑跨越式發(fā)展故事。
500兆瓦級巨型沖擊式水電機組研制實現(xiàn)里程碑式突破
中國每4度電就有1度源于東方電氣的裝備,其研制的發(fā)電裝備約占中國總裝機容量1/4。
1981年,東方電機為萬里長江第一壩——葛洲壩水電站研制的兩套單機容量為170兆瓦的水輪發(fā)電機組成功投產(chǎn)。1985年,葛洲壩機組榮獲中國水電史上首個“國家科學技術進步獎特等獎”。
值得一提的是,葛洲壩170兆瓦的軸流轉槳式水輪發(fā)電機組其11.3米的轉輪直徑至今仍然保持世界之最。
白鶴灘水電站裝機總容量1600萬千瓦,左右兩岸分別安裝8臺單機容量100萬千瓦的水電機組,左岸全部8臺機組由東方電機自主研制供貨。而這臺單機容量100萬千瓦的發(fā)電機組,實現(xiàn)了100%國產(chǎn)化率。機組轉動部件重達2600噸,由上萬個零部件構成,實現(xiàn)了“零配重”,機組穩(wěn)定性好,擺度僅僅一根頭發(fā)絲直徑大小。
高水頭大容量沖擊式水電機組是服務國家“加快西南水電基地建設”的主力機型。受應用市場缺乏、研發(fā)投入不足等因素影響,我國高水頭大容量沖擊式水電機組自主研制水平薄弱,與國外先進企業(yè)存在差距。
2019年開始,東方電機全力組織開展高水頭大容量沖擊式水電機組關鍵技術研究,聯(lián)合科研院所、上下游企業(yè),針對梳理出的涉及水力、水機、電機、工藝4大專業(yè)的70多項攻關課題開展聯(lián)合技術攻關。
2020年,東方電機成功建設具有世界先進水平的沖擊式水力模型試驗臺,具備了沖擊式水電機組轉輪水力開發(fā)的能力。同時,具備了高水頭大容量沖擊式水電機組轉輪研制能力。
2023年6月7日,東方電機自主研制的150兆瓦大型沖擊式轉輪在四川田灣河流域金窩電站實現(xiàn)工程應用,為國內在運單機容量最大的沖擊式水電機組裝上“中國心”,目前該轉輪已安全穩(wěn)定運行100多天。
500兆瓦沖擊式水電機組是世界單機容量最大的沖擊式水電機組,入選國家能源局能源領域首臺(套)重大技術裝備。
2023年8月31日,東方電機聯(lián)合產(chǎn)業(yè)鏈上下游企業(yè)國機重裝、中信重工研制的扎拉水電站世界首臺單機容量最大功率500兆瓦沖擊式水電機組轉輪中心體鍛件全面通過大唐集團業(yè)主驗收,實現(xiàn)了500兆瓦級高水頭大容量沖擊式水電機組研制里程碑突破,開啟我國水力發(fā)電產(chǎn)業(yè)高質量發(fā)展新篇章。
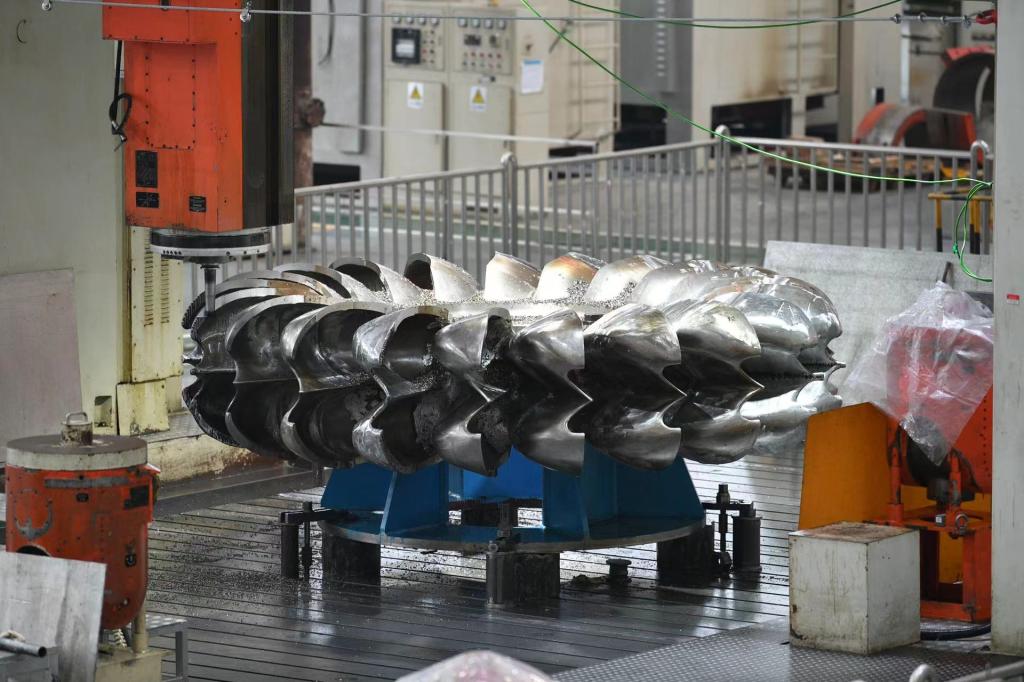
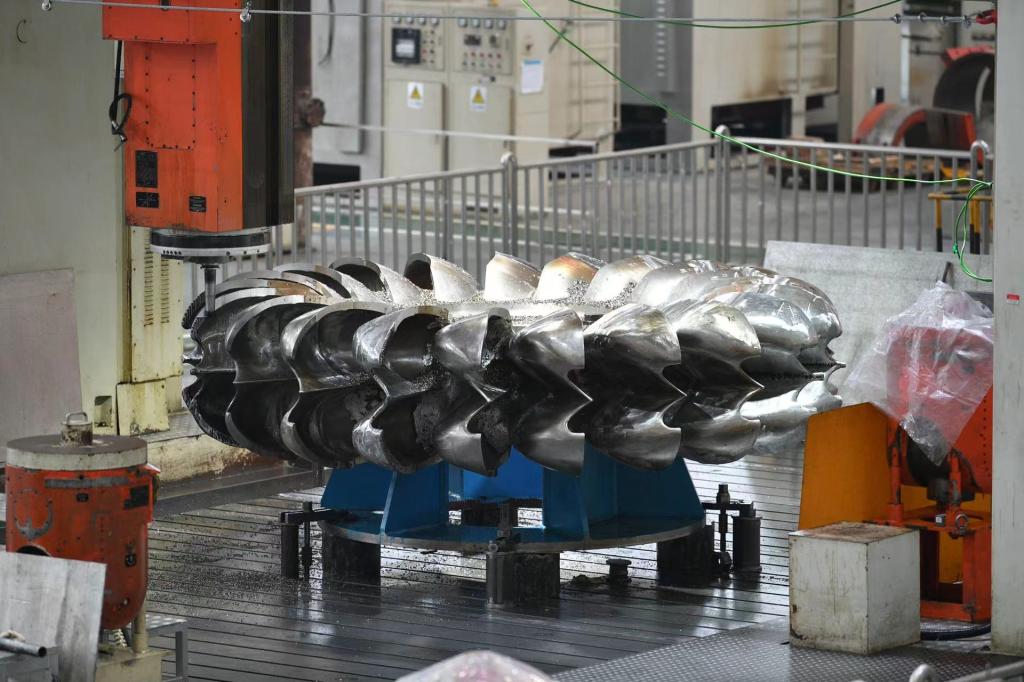
國產(chǎn)首臺150兆瓦級大型沖擊式轉輪 東方電氣供圖
行業(yè)5G全連接數(shù)字化工廠
走進東方電機大型清潔能源裝備重型制造數(shù)字化車間,這里已經(jīng)是重型機加控制、數(shù)字化裝配、機器人焊接等為一體的新一代清潔能源裝備重型制造車間。
該車間實現(xiàn)數(shù)字孿生功能,打造機器人智能焊接集群,將焊接技術與5G、自動化控制及物聯(lián)網(wǎng)技術有機融合,大幅改善焊接工人的工作環(huán)境,提高焊接質量和焊接效率。
值得一提的是,機器人智能焊接集群已廣泛應用于實際生產(chǎn),完成了白鶴灘、長龍山、國產(chǎn)化首臺套150兆瓦沖擊式轉輪等重大項目核心部件焊接,焊接產(chǎn)品質量優(yōu)異,實現(xiàn)了“臺臺精品”。
在東方電機大型清潔能源裝備重型制造數(shù)字化車間,重型機加控實現(xiàn)了數(shù)字孿生功能,車間機臺操作者可以通過現(xiàn)場終端實現(xiàn)開工、報工、質檢、圖紙技術資料查閱、起吊呼叫、刀具配送呼叫、輔助操作呼叫、視頻監(jiān)控、異常報警、數(shù)據(jù)實時顯示等功能,產(chǎn)品加工效率和質量大幅提升。
在定子沖片綠色“無人”車間,可以發(fā)現(xiàn),車間已經(jīng)完全融入5G、互聯(lián)網(wǎng)、物聯(lián)網(wǎng)、機器視覺等技術,結合數(shù)字化運營管理,實現(xiàn)了生產(chǎn)操作無人化、生產(chǎn)數(shù)據(jù)驅動化、生產(chǎn)控制智能化、生產(chǎn)產(chǎn)品綠色化。
東方電機數(shù)字化與智能制造技術部副部長李浩亮介紹說,定子沖片綠色“無人車間”將定子沖片產(chǎn)量從9000噸提高到15000噸,人均產(chǎn)出提升620%、能源利用率提高56.6%、勞動強度降低90%以上,揮發(fā)性有機排放降低70%以上,定子沖片的產(chǎn)品質量和生產(chǎn)效率大幅提升。
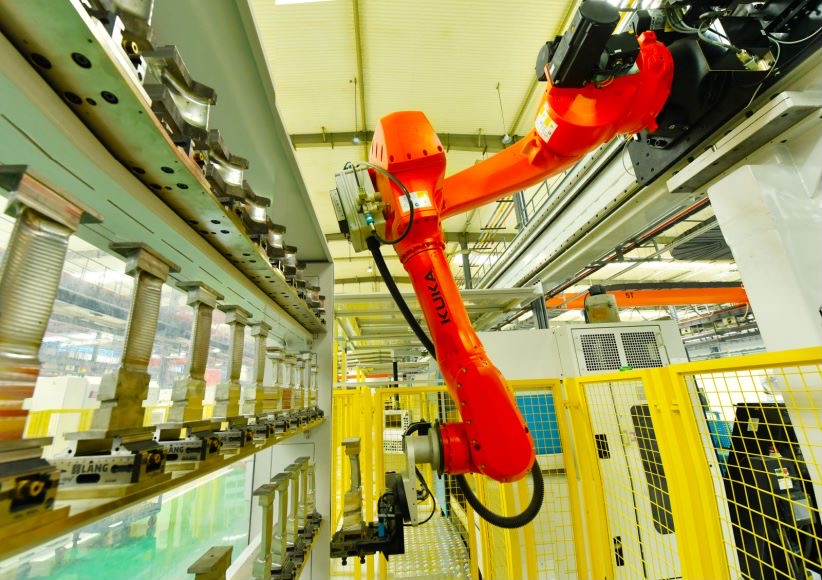
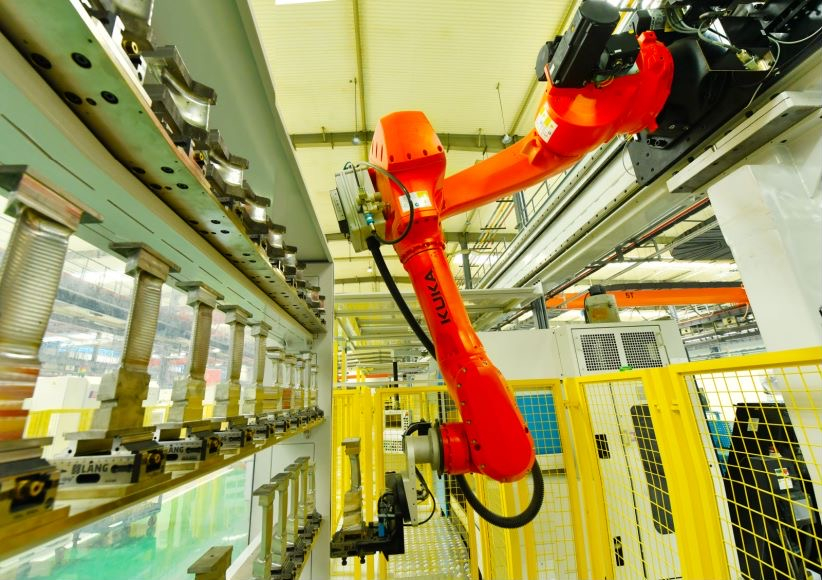
國內首個葉片加工無人車間及黑燈產(chǎn)業(yè)鏈 東方汽輪供圖
誕生新時代“爭氣機”
肩負著將內能轉化為機械能的重要使命,汽輪機一直是發(fā)電設備中最復雜精密的部分。作為東方電氣旗下的又一重要子公司,東方汽輪機通過數(shù)字化轉型,將汽輪機制造水平推上了新的高度。
今年8月,東方汽輪機在行業(yè)內率先實現(xiàn)人員、資源、技術、制造、產(chǎn)品等全域數(shù)據(jù)的互聯(lián)互通,每日處理數(shù)據(jù)超500G,成為行業(yè)首個5G全連接數(shù)字化工廠。目前,東方汽輪機已建成9個數(shù)字化車間21條智能生產(chǎn)線,以5G+工業(yè)互聯(lián)網(wǎng)為底座實現(xiàn)企業(yè)運營的數(shù)據(jù)驅動。
在葉片數(shù)字化車間,機器人、AGV、加工中心、三坐標檢測設備等高效協(xié)同、有序運行,行業(yè)內首次實現(xiàn)物流、加工、檢測全流程無人干預、連續(xù)運行,人均效率提升650%,質量合格率達99%,東方汽輪機通過數(shù)字化轉型建立起行業(yè)首條葉片加工黑燈產(chǎn)線,打造出行業(yè)首個葉片加工無人車間。
在焊接數(shù)字化車間,以窄間隙智能焊接、多機器人協(xié)同焊接、焊縫AI檢測、5G+焊接數(shù)采等關鍵技術的應用,東方汽輪機建成國內首個綠色高效焊接數(shù)字化車間,使生產(chǎn)效率提升300%,每年直接碳減排380余噸,引領行業(yè)開啟零缺陷、零排放、零變形的“三零”焊接新模式。
在總裝數(shù)字化車間,東方汽輪機打破傳統(tǒng)的實物總裝模式,將數(shù)字測量與傳統(tǒng)裝配技術相結合,開發(fā)總裝通流預測軟件,解決超大件裝配時測量難裝配難的問題,建成行業(yè)首個總裝數(shù)字化車間,使汽輪機總裝周期縮短40%。
東方汽輪機數(shù)字化與智能制造部副部長易泰勛介紹說,通過數(shù)字化轉型的升級改造,東方汽輪機實現(xiàn)了傳統(tǒng)制造向數(shù)字制造的完美蛻變,公司不僅在生產(chǎn)制造上持續(xù)升級,還建立起供應商、企業(yè)、客戶相互協(xié)同的數(shù)字化供應鏈,開展產(chǎn)品遠程監(jiān)測和智能運維服務,實時監(jiān)控園區(qū)安全、能源、環(huán)境數(shù)據(jù),使生產(chǎn)效率大幅提升,制造成本不斷降低,產(chǎn)品質量持續(xù)改善。
2022年底,東方汽輪機成為國內行業(yè)首家通過智能制造成熟度三級認證的企業(yè),在數(shù)字化轉型的道路上走在了時代前沿。與此同時,由東方汽輪機自主研制,國內首臺具有自主知識產(chǎn)權的F級重型燃氣輪機(代號G50)在這個5G全連接數(shù)字化工廠順利下線發(fā)運,翻開了我國自主重型燃氣輪機的新篇章,G50也成為我國新時代“爭氣機”的代名詞。
打破70多年技術封鎖,中國“爭氣機”G50研制成功
當今,全球只有美國、德國、日本、意大利 4個國家完整地掌握了燃機研發(fā)技術,并作為其長期優(yōu)先發(fā)展、進行嚴密技術封鎖的高端戰(zhàn)略性裝備。
燃氣輪機用途廣泛,例如電廠發(fā)電、園區(qū)分布式能源冷熱電三聯(lián)供、西氣東輸管道氣增壓驅動、艦船驅動等,具有高效率、低污染、啟??臁⒂玫厣俚纫幌盗袃?yōu)點。
為了打破70多年的技術封鎖,研制東方電氣集團G50重型燃氣輪機的田曉晶博士與團隊,攻克了燃氣輪機難題。
田曉晶介紹說,目前我國正在運行的各種燃氣輪機超千臺,幾乎全部由上述 4個國家所提供。在與我國合資、合作過程中,美國、德國、日本、意大利這四個國家僅轉讓冷卻部件制造和裝配技術,最核心的高溫部件被牢牢把控。燃氣輪機也是我國典型的 “卡脖子”關鍵核心技術?!?/p>
“燃機中的高溫部件每隔一段時間就需要維修和替換,基本只能由原燃機供應廠商提供,具有絕對的定價權?!碧飼跃дf。
當前我國燃機市場和維修均沒有掌握在自己手中,而當前復雜的國際環(huán)境形勢,要求我們必須要有自主的燃氣輪機。
為了主動服務國家戰(zhàn)略,東方電氣集團東方汽輪機有限公司在2009年啟動了F級50MW重型燃機項目,簡稱G50,經(jīng)過14年的堅持,2023年3月8日,依托國家能源局首臺套重大技術裝備項目,G50在廣東清遠順利通過96h商業(yè)運行考核,標志著G50研制成功。
東方電氣實現(xiàn)了國產(chǎn)燃機從無到有的突破。G50也被譽為中國 “爭氣機”,分別于2020年和2022年兩次入選國資委評選的“央企十大國之重器”。
G50是國內首臺完全正向自主設計、制造、試驗的 F級燃氣輪機,打破了70多年的技術封鎖,為我國能源體系的安全貢獻了力量。
田曉晶介紹,通過G50的研制,東方汽輪機目前已經(jīng)搭建了自主F 級燃機設計體系,已獲授權發(fā)明專利136項,具備了燃機全部部件的制造能力。
田曉晶感慨地說,14年的潛心研發(fā),終于啃下了重型燃氣輪機國產(chǎn)化這塊“硬骨頭”,填補了自主燃氣輪機應用領域的空白。
專利創(chuàng)造之路上從來沒有坦途和捷徑,只有不避艱險、不怕困難,敢于面對挫折和失敗,才能勇攀技術高峰。東方電氣集團培養(yǎng)和帶動燃氣輪機相關產(chǎn)業(yè)鏈上下游創(chuàng)新型企業(yè)300多家,實現(xiàn)了2萬多個零部件全部國產(chǎn)化,保障了產(chǎn)業(yè)鏈的自主可控。
“未來,我們將繼續(xù)走自主創(chuàng)新之路,提高國產(chǎn)燃機技術先進性,助力國產(chǎn)燃機取得更大的輝煌。”田曉晶說。